With a 2022 turnover exceeding €1 billion and a global workforce of 2,177, the SIAD Group has established itself as a formidable and respected industrial force. The company serves over 70,000 customers globally, demonstrating a broad operational footprint across various sectors, including petrochemical, chemical, energy, refinery, food and beverage, and industrial gases. In the realm of engineering, SIAD specialises in the design and manufacture of air separation units for producing industrial gases, small-scale LNG plants, reciprocating compressors for processing gases and air, plants for CO2 production, purification and liquefaction, biogas upgrading systems, and industrial burners, among other things.
Delving deeper into the SIAD Group’s diverse portfolio, the company’s involvement in the hydrogen value chain stands out as a key area of expertise. SIAD plays an instrumental role in various critical stages of this chain, including hydrogen production, storage, and distribution, as well as advising customers on hydrogen use and applications. In addition, SIAD also produces hydrogen-ready combustion systems. Furthermore, SIAD’s proficiency in hydrogen compression technology is essential for hydrogen use and effective storage in cylinders, as well as its transportation via tube trailers and hydrogen pipelines, some of which are also operated by SIAD to ensure efficient delivery to end-users.
SIAD Group’s unique value proposition for H₂ compressors
The company manufactured its first hydrogen compressor in 1953. Today, hydrogen ranks as the primary gas handled by SIAD compression equipment, a fact underscored by more than 500 of its hydrogen compressors currently operating worldwide. This extensive experience not only highlights SIAD’s capability in addressing the needs of the hydrogen market but also underscores its important role in shaping the hydrogen ecosystem.
“Our involvement in the entire hydrogen value chain is a major advantage, something none of our competitors offer,” says Mr. Gadkary. “We have the unique capability of not only producing hydrogen but also providing compressors that perfectly align with hydrogen production and the needs of our customers. Moreover, our experience dates back to the 1950s, encompassing millions of hours of operational expertise. This aspect is crucial, especially for new players in the industry. As the market grows and new companies emerge, having a partner well-versed in hydrogen technology and its value chain becomes invaluable.
“Our involvement in the entire hydrogen value chain is a major advantage.”
“Additionally, our in-house hydrogen production facilities enable us to conduct extensive testing – a capability many other players lack, adds Mr. Gadkary. “These factors collectively define our unique value proposition and how we aim to differentiate ourselves in the market.”
Driving innovation to support energy transition
In its relentless commitment to innovation, SIAD has recently achieved a significant milestone in compressor technology with the development of a new high-pressure, oil-free compressor capable of reaching up to 550 bar. This innovation builds upon SIAD’s historical portfolio, enhancing the company’s ability to meet the evolving needs of the industry.
“Our latest high-pressure compressor specifically targets the transportation and mobility markets, which are two of our key focus areas,” explains Mr. Gadkary. “In transportation, this innovation supports the use of higher-pressure cylinders and tube trailers, capable of storing more product and thereby more efficiently utilising their capacity. Until recently, cylinders and tube trailers typically carried pressures of 200–250 bar. Now, with the advent of composite materials, they can handle pressures up to 500 bar, and our new compressor is designed to achieve this higher pressure range.”
Furthermore, with this new compressor, SIAD is making a strategic entry into the hydrogen refuelling station market, which is also characterised by high-pressure requirements.
Pushing the envelope
Particularly in applications where high hydrogen purity is a stringent requirement, such as mobility, oil-free compressors are essential because any trace of oil contamination in hydrogen can be detrimental, leading to compromised fuel cell performance and potentially hazardous situations. Therefore, ensuring oil-free compression is not only a technological advancement but also a critical safety and performance consideration.
“We have been continually pushing the envelope in our field,” says Mr. Gadkary. “In the past, oil-free technology was limited to lower pressure ranges, while lubricated compressors were the norm in higher pressure ranges. Our expertise in oil-free technology is well established, but what is new is how we have extended this know-how to higher pressures, transitioning from oil-free technologies operating at pressures of around 100 bar to an impressive 550 bar.”
As Mr. Gadkary explains, this advancement stems from improvements in multiple areas of engineering. A critical aspect of this evolution has been the adoption of advanced materials, transitioning from PTFE to high-performance alternatives such as PEEK and other polymers. This innovation required a complete rethinking of materials of construction, sealing systems, and piston geometries to effectively adapt to the higher pressures and broaden the company’s application scope.
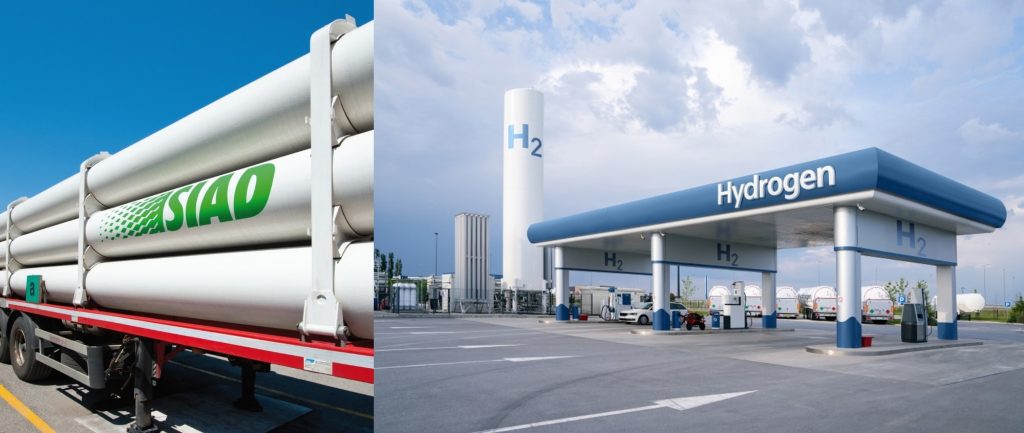
Lowest total cost of ownership (TCO)
In its endeavour to provide customers with the most cost-effective solutions, the SIAD Group adheres to a comprehensive set of criteria guiding its innovations. Foremost among these is compressor efficiency, a critical factor directly influencing energy costs. This underscores the paramount importance of energy efficiency in the company’s designs.
“Our compressors are renowned for their flexible and uninterrupted operation, characterised by exceptional energy efficiency,” proudly states Mr. Gadkary.
“Reliability follows closely, recognising the pivotal role it plays in enabling the maintenance or reduction of operational costs,” he continues. “We also diligently adhere to a myriad of regulations, with a strong emphasis on harmonised standards, especially vital in high-pressure applications such as those in the mobility sector, ensuring that our products consistently align with the most stringent safety measures.
“Equally significant is equipment availability, recognising that a compressor’s worth is truly realised when it remains operational. To this end, our compressors boast an impressive mean time between overhauls of 8,000–12,000 hours, ensuring extended uptime. Moreover, we place a premium on the maintainability of our compressors, ensuring that maintenance procedures are straightforward, without the need to disassemble a significant portion of the unit.”
“Our compressors boast an impressive mean time between overhauls of 8,000–12,000 hours.”
To encapsulate these vital considerations, Mr. Gadkary refers to them as ER²AMP – Efficiency, Reliability, Regulations, Availability, Maintainability, and Power Density. Following these principles enables SIAD to provide compressors that strike the optimal balance between capital and operational expenditures. “Ultimately, this design philosophy leads to a substantial reduction in the total cost of ownership for our valued customers,” he says.
Rigorous approach to product development
In the development process for its high-pressure compressor, the SIAD Group involved its customers, industrial partners, and academia, using a very rigorous approach.
Mr. Gadkary explains: “Our marketing and business development teams were closely attuned to the voice of the customer. We adopted the Six Sigma DMADV (Define, Measure, Analyse, Design, and Verify) approach, which is invaluable for implementing new strategies, as it identifies success factors early and relies on data-driven analysis.
“We conducted dynamic testing on our shop floor, followed by an endurance test at our hydrogen production plant. This testing process ensured the practicality and viability of the compressor.
“Our design leveraged the latest technologies, incorporating the concept of digital twins, and we collaborated with universities and industrial suppliers throughout the development process. Initial tests involved helium, and we have now progressed to testing with hydrogen, leveraging SIAD’s hydrogen production capabilities. The result is a fully realised product, rigorously tested and successfully commercialised in the market.”
Hydrogen Rising Star Company of the Year
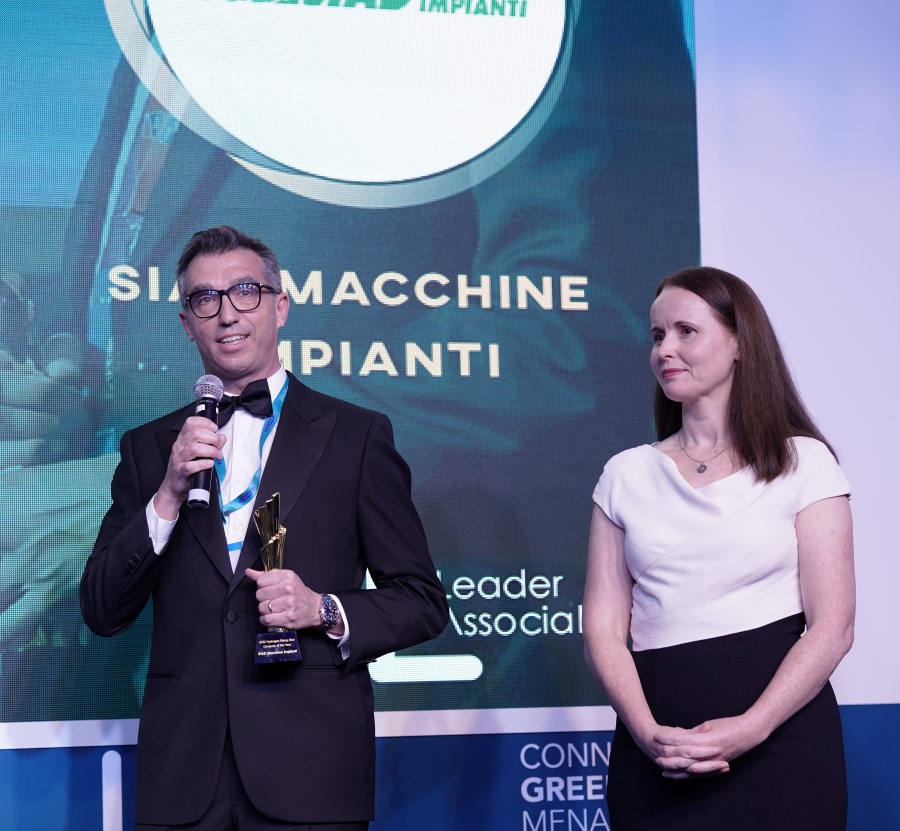
Safety: a paramount priority
The SIAD Group places paramount importance on the safety of its compressors, a commitment reflected in their impressive track record. With more than 500 hydrogen compressors currently operational and over 25 million hours of running time, the company has garnered extensive experience in ensuring safety. The SIAD Group’s gas sector has been a long-time active member of the European Industrial Gas Association (EIGA) and has more recently joined the Compressed Gas Association (CGA) and the Asian Industrial Gas Association (AIGA), adhering to stringent industry standards.
SIAD’s hydrogen compressors are designed with an array of robust safety features, including a total leak-free design and high-quality materials and components. Additionally, the company collaborates with premium suppliers for instruments and safety devices, guaranteeing the highest standards of quality and reliability. The compressors are equipped with full process monitoring systems that continuously oversee operations to detect and address any issues promptly. In the event of anomalies, a fail-safe stop procedure is implemented to automatically shut down the system and prevent accidents. Furthermore, the compressors feature secure automatic depressurisation to safely reduce system pressure and avoid hazardous scenarios. Regular hazard and operability studies (HAZOP) and risk analysis are conducted to anticipate and mitigate potential risks, underscoring SIAD’s commitment to safety in their hydrogen compression solutions.
Projects, partnerships, and vision
Recent and upcoming green hydrogen projects incorporating SIAD’s hydrogen compressors include a 20 MW electrolysis plant at the Ovako rolling mill in Hofors, Sweden; world’s first high-temperature electrolyzer system on a multi-megawatt-scale at Neste’s renewable products refinery in Rotterdam, the Netherlands, and a major project in Western Europe (see box ‘Project in Western Europe’).
In September 2022, SIAD signed a framework agreement with the electrolyser manufacturer Nel for the supply of hydrogen compressors. This agreement complements the company’s existing collaborations and partnerships with a host of major global EPC contractors, end users, as well as electrolyser and fuel cell companies.
Project in Western Europe
While actively expanding its client base, SIAD is simultaneously exploring advancements in its hydrogen compressor offerings to meet even higher pressure requirements, through the adoption of hybrid technologies.
“Our development process is ongoing and evolving,” explains Mr. Gadkary. “At present, our piston reciprocating compressors are capable of reaching up to 550 bar, but we are not stopping there. We are exploring hybrid technologies to push these boundaries further. In our reciprocating compressors, there is a central stream that remains vacant, and here, we see potential for integrating diaphragm technology. By creating a hybrid system, we aim to extend the pressure capacity from 550 bar to 700 bar or even higher. This thought process reflects our continuous commitment to actively respond to the market’s evolving needs, especially in the mobility sector where pressures of 700 bar and above are becoming increasingly relevant.
“However, this is not just about meeting market demands; it is about supporting the shift towards cleaner energy and fuel cells,” concludes Mr. Gadkary.