The rise of hydrogen projects
There has been a surge in industrial clean and low-carbon hydrogen projects over the last few years, thanks to significant reductions in the costs of hydrogen production, storage, and distribution technologies. Additionally, new policies, such as the US Clean Hydrogen Production Tax Credit1 under the Inflation Reduction Act, have catalyzed the adoption of clean hydrogen. As of the end of January 2023, over 1,000 large-scale clean and low-hydrogen projects have been announced globally, 795 of which plan full or partial operation by 2030.2 The total investment in these projects is estimated to be around US$ 320 billion, a positive sign for the clean energy transition. However, only $29 billion has passed the final investment decision (FID). The remainder of the investment is still tentative and will likely undergo revisions following various stages of feasibility analyses and front-end engineering loading design. While the potential of hydrogen is recognized by industries, final investment decisions are often delayed because clean-hydrogen technologies are expensive and not yet fully de-risked. In this article, I will share some perspectives on how to de-risk projects involving water electrolyzers.
Water electrolyzers: key to clean hydrogen
Water electrolyzers are extensively used to produce hydrogen by splitting water through the application of electrical power. When the electricity used is derived from carbon-free sources, the resulting hydrogen can be considered clean or zero-carbon. Due to the ubiquity of water, this method is widely used worldwide for producing clean hydrogen. Currently, three types of electrolyzers are commercially available: alkaline, proton-exchange membrane (PEM), and anion-exchange membrane (AEM). Additionally, solid oxide electrolyzers are undergoing pilot demonstrations. All commercial electrolyzers operate at low to moderate temperatures (30–80°C) and can integrate with intermittent renewable electricity sources with various degrees of flexibility. The three types of electrolyzers differ significantly in terms of technology, underlying scientific principles of operation, and the materials used. Their costs also vary substantially. In 2023, the total installed cost (TIC) for electrolyzers was reported to range between $1,700 and $2,000, approximately 10% higher than that in 2022 due to inflation.3 The lower end of this estimate is for alkaline electrolyzers, and the upper end for PEM. Data on AEM electrolyzers is limited as they are newer to the market. The TIC includes equipment costs for electrolyzers, gas purifiers, transformers, rectifiers, and related components, as well as expenses foe engineering, construction labor, project development, interconnection agreements, insurance, etc.
Challenges in electrolyzer project development
There are several factors hindering the development of electrolyzer projects and slowing down investment decisions. The primary factor is the high capital costs associated with electrolyzers. However, the manufacturing price of electrolyzers has been gradually declining over the years, except for the last couple of years, due to COVID-19 pandemic-related supply chain issues and global inflation. Owing to the number of projects in the pipeline, various policy incentives, and an increase in manufacturing volume, the TIC for electrolyzers is expected to drop to the $500–$1,000/kW range by 2030. More original equipment manufacturers are entering the market with innovative designs. I believe that the reduction in electrolyzer prices is on a good track to contribute significantly to achieving our net-zero targets in the coming decades.
Standardization: a path to risk mitigation
One crucial aspect for de-risking electrolyzer projects is the standardization of electrolyzers. Currently, electrolyzers from different manufacturers vary in design, shape, size, and integration within hydrogen production plants. This variation means project developers cannot guarantee that stacks from one manufacturer can be seamlessly replaced by those from another. If the electrolyzers come from a large, financially stable company, this issue is less pronounced. However, the market is seeing an influx of startups with innovative electrolyzer designs. Despite the uniqueness and appeal of their products from a design and engineering perspective, the financial stability of these startups is often uncertain, leading to increased insurance costs. Ensuring that stacks from smaller manufacturers can be replaced with those from larger, established companies in the event of bankruptcy would significantly reduce project risks and insurance costs. I believe that professional hydrogen associations should implement a set of standards for electrolyzer manufacturers in the future.
Establishing bankability of electrolyzer products
An important method for de-risking new technologies involves thorough assessments by third-party engineering firms. Startups entering the market can greatly benefit from this, as it provides credibility to their unestablished products. Investors, project developers, and insurance companies often seek independent evaluations of design, performance, manufacturing processes, quality control procedures, warranties, product support strategies, and the company’s structure to determine the bankability of the product and its manufacturer. At Black & Veatch, we have been conducting independent assessments of clean-energy technologies for over a decade, with many manufacturers benefiting greatly from these reports.
Assuring safety and compliance
In addition, the manufacturers should also have proper knowledge about the design safety rules (e.g., National Fire Protection Association or NFPA rules in the US) and the certifications (e.g., UL certifications) for their products to be considered for projects. From my experience, many electrolyzer companies failed in the past in terms of design safety that comply with the regulations, such as, NFPA rules which are essential for projects in the US. An experienced engineering firm like Black & Veatch can help electrolyzer manufacturers navigate this complex landscape efficiently.
Partnering with large engineering firms
In addition to the safety and compliance issues, many electrolyzer manufacturers have struggled to demonstrate effective and reliable post-installation product support strategies. A viable approach for smaller companies is to collaborate with engineering firms that have the required expertise to manage post-installation operations and maintenance on their behalf. Black & Veatch, for example, have been involved in more than 1 GW electrolyzer projects all over the world, and are currently establishing partnerships with electrolyzer manufacturers to provide post-installation product support services included in the warranty. For smaller companies or foreign manufacturers with less manpower in a certain country can benefit from these partnerships.
Following these guidelines, electrolyzer technologies from different manufacturers can be de-risked for project deployment and will eventually catalyze the hydrogen economy and mitigate the effects of climate change. As electrolyzers are expensive and there are significant safety risks associated with hydrogen, electrolyzer manufacturers should use the above-mentioned strategies to de-risk their products.
Notes and references
*Note: Opinions expressed in this article are solely my own and do not represent those of my employer, Black & Veatch.
2 Hydrogen Council and McKinsey & Company. (2023). Hydrogen Insights 2023.
About the author
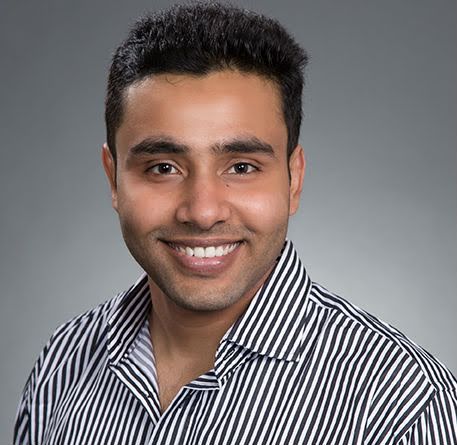
Dr. Prantik Saha is a strategy consultant at Black & Veatch, with domain expertise in green hydrogen, low-carbon fuels, utility-scale battery energy storage, and long-duration energy storage technologies. With over six years of experience in technology development (R&D), he provides advisory services to help clients achieve their decarbonization goals. He also assists in conceptual project design, early-stage front-end engineering loading (FEL), feasibility analysis, due diligence, independent technology assessment (bankability), and integrated resource planning for several clean energy projects. He obtained his Ph.D. in Applied Physics, focusing on clean energy systems, at the University of California, Irvine. He also leads the hydrogen and energy storage sections of the Climate & Sustainability Taskforce at the Institute of Electrical & Electronics Engineers (IEEE).
Email: sahap@bv.com