Technological advancements and improvements in industry practices, such as green hydrogen and direct electrification, offer opportunities for immediate decarbonization steps. From augmenting energy efficiency to fostering supply chain collaboration, steel companies are already implementing measures that not only contribute to global decarbonization targets but also bolster operational efficiency, build resilience, and drive long-term sustainability. This article will delve into strategies for tangible near-term action and spotlight companies already making significant strides toward a greener steel industry.
The economic equation
For decarbonization solutions to be sustainable from a business perspective, particularly in the current business climate, they must offer robust economic value. However, economic benefits extend beyond immediate cost savings or operational efficiencies. Decarbonization actions also future-proof operations against shifts in regulation, demographics, or resource scarcity.
In the near term, simple payback calculations, driven by low-cost energy, may discourage investment in decarbonization. However, the economics of emissions reduction are not static. As societal awareness and concern about climate change intensify, regulations will likely tighten, and consumer behavior will become more conscious. Disruptions in fossil fuel supply due to global instabilities could impact fuel costs and, ultimately, energy prices. These risks are also critical to economic analysis, even in the near term. Companies that prioritize decarbonization now are more likely to stay ahead of emerging trends, maintaining their competitive advantage while also contributing positively to global decarbonization efforts.
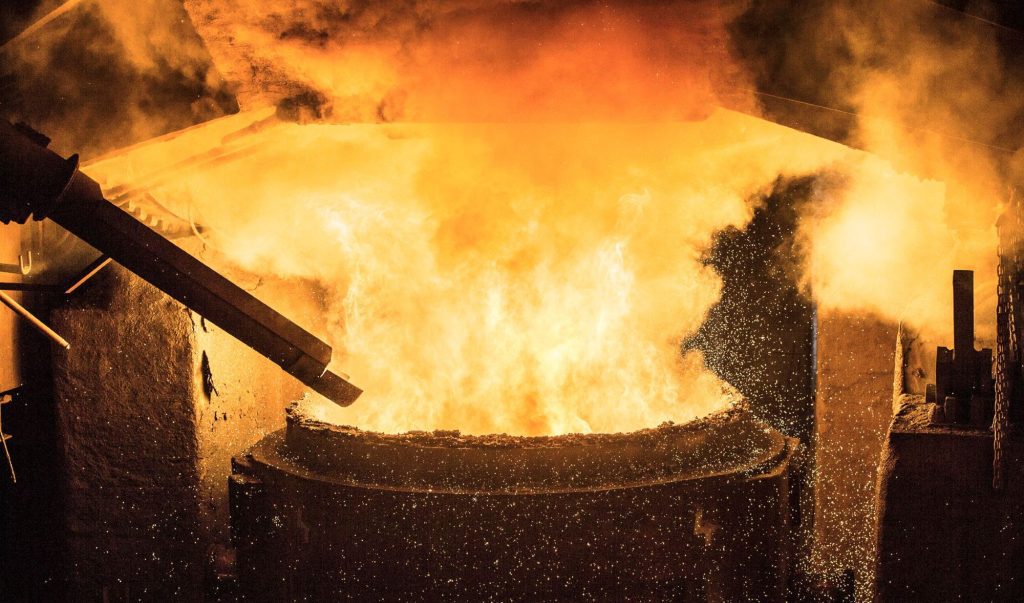
Striking a balance
For near-term decarbonization strategies to positively impact the bottom line, whether by reducing costs, opening new revenue streams, or future-proofing against likely regulatory and market shifts, they must focus on strategic actions that are both effective and pragmatic. The following sections will explore such actions that are already making a significant impact on the steel industry’s decarbonization journey.
First steps for hydrogen-based steel production
Green hydrogen is emerging as a pivotal solution for decarbonizing steel, serving as a reducing agent to produce iron sponge in direct reduction of iron (DRI) towers. However, uncertainties remain concerning green hydrogen, such as whether it should be produced on-site or imported, the optimal design for hydrogen plants, and the potential requirement to integrate DRI systems with existing steel mills. To address these uncertainties and gather crucial insights, Swedish steel entities like Ovako (a subsidiary of Nippon Steel), SSAB through its Hybrit initiative, and the start-up H2 Green Steel have taken pioneering steps. For instance, Hybrit’s pilot plants, Ovako’s on-site hydrogen production combined with current steel mills, and H2 Green Steel’s comprehensive green facilities (encompassing hydrogen production, DRI, and steel mills) offer glimpses into the feasible pathways available today.
Embracing electric arc furnaces
Many steel plants have transitioned from traditional blast furnaces to electric arc furnaces (EAFs). The EAF market has experienced steady growth over an extended period of time, with the Global Steel Plant Tracker reporting a 68% increase in 2023 compared to the previous year.1 EAFs, which primarily utilize recycled steel scrap, are not only more energy-efficient but also generate significantly fewer carbon emissions than blast furnaces. The effectiveness of this transition as a decarbonization strategy can be amplified in regions where the electricity grid is already low-carbon or transitioning toward renewables. Recently, UK Steel announced a £1.25 billion investment in adopting two electric arc furnaces, reducing its CO2 intensity by around 75%.2

Enhancing energy efficiency
The most direct way to reduce carbon emissions while reducing operating costs is reducing energy consumption in the production process. There are mature technologies and methods that steel plants can consider.
Technology upgrades can improve energy efficiency through the replacement of older machinery with newer, energy-efficient models or by updating data acquisition systems to better monitor and manage energy usage. Existing equipment and operating procedures can be modified to use less energy through the implementation of advanced controls that ensure equipment runs at peak efficiency and uptime. Simple improvements, such as regular maintenance, can yield dividends by ensuring machinery operates reliably and uses less energy.
Steel manufacturing processes generate a significant amount of heat, much of which is wasted in legacy steel plants. By recovering and reusing waste heat, steel plants can reduce their dependence on external energy sources. For instance, waste heat can be used to preheat inputs or can be converted into electricity to power other operations.
ArcelorMittal, the world’s largest steel company, developed ‘Energize’, a group-wide energy efficiency program that identified 200 potential projects with energy-saving potential. These projects spanned across the strategies mentioned above, demonstrating a broad spectrum of opportunities for energy efficiency in the steel industry.
Endless casting and rolling
Endless casting and rolling is an innovative process that combines the traditional two-step process of casting billets and rolling them into final products into a single, continuous operation. Eliminating the need to reheat billets before rolling means this technology can significantly reduce energy consumption. Furthermore, the continuous nature of the process reduces yield losses and improves product quality, offering additional economic benefits.
A leading supplier in this field is Primetals Technologies, a joint venture of Siemens VAI, Mitsubishi Heavy Industries, and partners. Primetals has developed Arvedi ESP (endless strip production) technology that allows for the direct rolling of hot-rolled coils with thicknesses down to 0.8 mm. This technology not only reduces energy consumption by up to 45% but also significantly decreases CO2 emissions compared to conventional casting and rolling processes.
Optimizing material efficiency
By optimizing the use of raw materials, steel companies can reduce the need for carbon-intensive primary steel production. Utilizing more scrap steel in the production process, reducing waste, and improving product design strategies are all means to this end. POSCO, for example, has made efforts to reduce waste by recycling steel slag to produce cement and construction materials, thereby lowering emissions while opening potential new revenue streams.
Strengthening supply chain management
Collaboration with suppliers and customers to create a more sustainable value chain can also yield significant emission reductions. Producers can select suppliers who prioritize sustainable practices or help customers recycle products at the end of their life. Tata Steel has an initiative they term ‘SteelRecycle’, which promotes recycling in the value chain and strengthens relationships with customers and suppliers alike.
Hybrit project
In 2016, SSAB, LKAB and Vattenfall launched the HYBRIT (Hydrogen Breakthrough Ironmaking Technology) initiative with the aim of creating an entirely fossil-free value chain from mine to finished steel. Several significant milestones have already been achieved:
- In August 2020, the pilot facility for the production of fossil-free sponge iron in Luleå, Sweden, was commissioned.
- In March 2021, Gällivare in Sweden was chosen as the site of the HYBRIT Demonstration project, which includes the construction of a greenfield, full-scale plant for the direct reduction of iron ore using fossil-free hydrogen. The hydrogen will be produced via a 500 MW water electrolysis plant in Gällivare, using renewable electricity. Commissioning is scheduled for 2026.
- In May 2021, the construction of a pilot rock cavern storage facility for hydrogen gas began, adjacent to HYBRIT’s pilot facility for direct reduction in Luleå. The underground storage facility commenced operation in late summer 2022, storing hydrogen produced by water electrolysis using fossil-free electricity. The pilot plant has a storage capacity of 100 m3. At a later stage, a full-scale hydrogen gas storage facility measuring 100,000–120,000 m3 may be required, enabling it to store up to 100 GWh of electricity converted into hydrogen gas, which is sufficient to supply a full-sized sponge iron factory for three to four days.
- In August 2021, SSAB produced the world’s first fossil-free steel, using HYBRIT technology, e., reduced by 100% fossil-free hydrogen instead of coal and coke.
Fostering collaboration and coalition building
Partnerships with other organizations and governments can accelerate decarbonization efforts. The sharing of best practices, technology collaboration, and policy advocacy can amplify the impact of individual actions. The World Steel Association has been instrumental in fostering such collaborations by bringing together global stakeholders in the steel industry to work collectively toward sustainable development goals.
Investing in renewable energy
Investing in renewable energy for operational energy needs can lead to substantial emission reductions. This applies to both electricity and coal. Some steel companies are exploring on-site renewable energy generation, while others are leveraging power purchase agreements (PPAs) with renewable energy providers. For instance, Voestalpine AG, an Austrian steel company, has been investing in wind energy to power its operations, setting a benchmark in the industry. Some steel companies are developing biochar to replace coke in blast furnaces. ArcelorMittal has successfully trialed up to a 15% replacement of coal with biochar.3
The role of hydrogen in steel production
Decarbonizing steel production is a crucial step in reducing carbon emissions. Using electrolytic hydrogen instead of fossil fuels such as coke, coal, natural gas, liquified petroleum gas (LPG), fuel oil, and diesel fuel, can significantly reduce carbon emissions. The primary steel production processes that can be decarbonized with hydrogen include:
IRON ORE REDUCTION: Traditional steel production relies on the blast furnace method, which uses coke (carbon-rich) as a reducing agent to convert iron ore into iron. Hydrogen can replace coke in a process known as direct reduction. Hydrogen reacts with iron ore to produce water vapor and pure iron, releasing no carbon emissions.
ELECTRIC ARC FURNACES (EAF): EAFs are used to recycle steel scrap and refine iron. In some cases, natural gas is used to heat the furnace. Hydrogen can replace natural gas in EAFs to provide high-temperature heat without emitting carbon.
ROLLING AND FORMING: Hydrogen can also be used in the heating processes for rolling and forming steel into the desired shapes. This replaces the use of natural gas or other fossil fuels, further reducing emissions.
ANNEALING: Annealing is a heat treatment process used to improve steel’s properties. It typically uses natural gas or other fuels for heating. Hydrogen can be used for annealing, eliminating carbon emissions in this phase.
TRANSPORT: In some steel plants, hydrogen can be used as a fuel for vehicles, such as forklifts and transport within the facility. This reduces the reliance on fossil fuels for internal logistics.
Future actions and government partnerships
While immediate actions hold the key to initiating the decarbonization journey, the steel industry also awaits the emergence of several groundbreaking technologies. These technologies, albeit in nascent or experimental stages, hold immense promise not only to drastically reduce carbon emissions but also to revolutionize the entire steel-making process.
Hydrogen-based steel production
As mentioned earlier, hydrogen holds significant promise as one of the replacements for coking coal in steelmaking, thereby eliminating CO2 emissions from the steel production process. However, the application of this technology is currently restricted by the demand for high-quality iron ore, the upgrading of which is perceived to pose a challenge to the business case. The combination of pioneering projects like Hybrit and H2 Green Steel, initiated earlier this decade, and the development of robust hydrogen export infrastructure will provide valuable lessons that can drive the optimization of hydrogen plants, subsequently lowering hydrogen production costs. Consequently, investments in hydrogen-based DRI assets will be less risky.
Carbon capture, utilization and storage
Carbon capture, utilization and storage (CCUS) technology aims to capture CO2 emissions during steel production, securely store them, and prevent them from entering the atmosphere or, ideally, convert them into useful products. An example of a company testing CCUS technology is Tata Steel’s Jamshedpur plant in India, with its pilot projects in Europe exploring the feasibility of large-scale carbon capture and storage. In tandem, companies like Carbon Clean Solutions are working on methods to utilize the captured carbon in the production of chemicals, fuels, and materials.

Electrolysis of iron ore
One of the more futuristic technologies involves the electrolysis of iron ore, much like aluminum is currently produced. Companies like Boston Metal, with their molten oxide electrolysis process, aim to make steel production more efficient and significantly less carbon intensive. The technology holds significant promise as it is also applicable to lower-quality iron ore. However, it remains to be proven at scale.
The road to these advanced decarbonization technologies often comes with high upfront costs, technical challenges, and the need for continuous innovation. This is where strong government-industry partnerships can play a pivotal role. Governments can incentivize the adoption of these technologies through mechanisms such as tax credits, research and development grants, and subsidies to offset the costs of transitioning to these new technologies.
However, decarbonizing the steel industry does not need to wait for future technologies. There are immediate actions, such as green hydrogen pilot projects, that can contribute to emissions reductions while offering tangible economic benefits in the near term. By taking action, even if incremental, steel companies can enhance operational efficiency, resilience, and sustainability as a start on their journey toward a lower carbon future.