With such a potential shift in the green hydrogen landscape, electrolyzer market has the potential to reach a staggering ~2,000 GW by 2050. The sheer magnitude of this market potential necessitates a diverse array of electrolyzer technologies to facilitate the global green hydrogen revolution.
Among the multitude of electrolyzer technologies, one particular contender has been catching the eye of industry experts – solid oxide electrolyzers (SOECs). This high-temperature electrolysis technology presents some interesting opportunities in integration with heat-intensive applications. Approximately 75% of the 2050 demand for green hydrogen finds its niche in heat-intensive industrial processes. These heat-intensive applications, such as refining, industrial heat generation, and steel production, can involve on-site hydrogen production and utilization while integrated with SOECs to recover waste heat. In such contexts, solid oxide electrolysis (SOEC) emerges as the one of the most promising and viable long-term solution.
At present, the commercial hydrogen electrolysis market primarily relies on two established technologies: alkaline (AE) and proton exchange membrane (PEM) electrolysis. Both of these technologies operate at relatively low temperatures, differentiating them from SOEC.
SOEC process and materials
SOECs consist of a solid oxide ceramic electrolyte nestled between two porous electrodes. At elevated temperatures, typically between 700–900°C, the solid oxide electrolyte becomes conductive to oxygen ions (O2−). When an electrical voltage is applied across the electrolyzer, oxygen ions are transferred from the cathode to the anode through the electrolyte, facilitating the conversion of steam into hydrogen gas.

At the cathode, typically made from a perovskite material, oxygen ions and electrons react. The oxygen ions, sourced from the external electrical circuit, combine with electrons to form oxygen gas (O2). Simultaneously, electrons travel through the external circuit from the anode to the cathode, generating an electric current.
On the anode side, often composed of nickel or other conductive materials, water molecules split into hydrogen ions (H+) and oxygen ions (O2−). The hydrogen ions (H+) produced at the anode move through the solid oxide electrolyte to reach the cathode. This electrolyte material, Yttria-stabilized zirconia (YSZ), offers excellent ionic conductivity across a wide range of temperatures while blocking the flow of electrons. It also keeps fuel and oxygen separate and retains water while ensuring structural stability.
At the cathode, the hydrogen ions meet electrons from the external circuit to produce hydrogen gas (H+). Overall, the electrochemical process effectively breaks water down into its two constituent elements: hydrogen and oxygen.
In the electrode sandwich, other materials play a supporting role. For less demanding applications, the oxygen electrode uses strontium-doped lanthanum manganite (LSM) material, while more demanding situations call for Lanthanum strontium cobalt ferrite material.
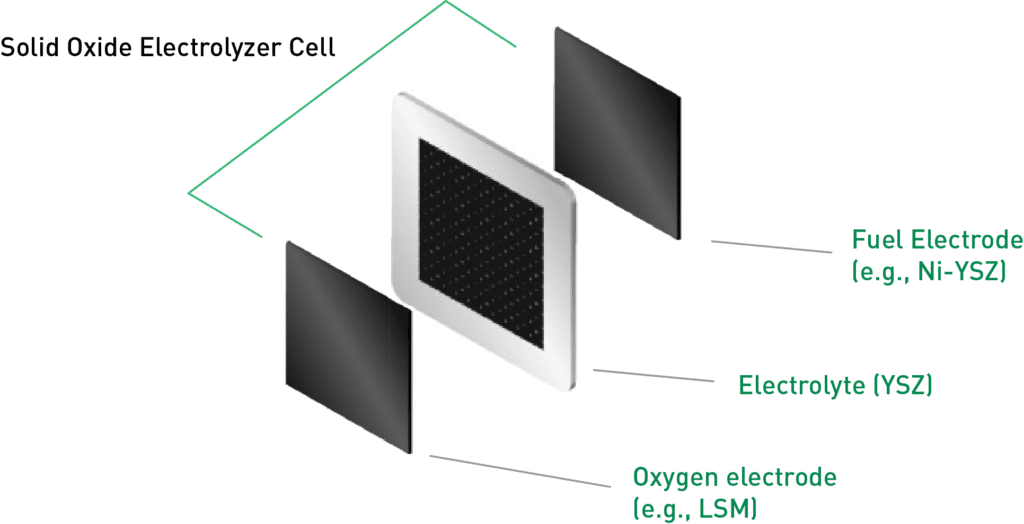
For fuel-based electrodes, one standout material is nickel-doped Yttria-stabilized zirconia (Ni-YSZ) composite. This selection is driven by several key factors: its high porosity, which supports the smooth flow of reactants; its exceptional electrocatalytic activity; its ability to conduct both ions and electrons (mixed ionic and electronic conductivity); and its compatibility with the solid oxide electrolyte, preventing undesirable reactions with electrolyte materials. These qualities collectively contribute to the efficiency and reliability of solid oxide electrolyzers.
Efficiency
SOECs set themselves apart from their counterparts, like PEM and alkaline electrolyzers, by operating at substantially higher temperatures, typically between 700–900°C. This temperature difference provides SOECs with a fundamental advantage – improved electrochemical efficiency.
These elevated temperatures translate to higher efficiency, a crucial factor in the pursuit of reducing the levelized cost of hydrogen (LCOH). Greater efficiency means producing more hydrogen per unit of electricity input, making the process both cost-effective and environmentally friendly.
SOEC electrolyzer efficiencies currently stand at approximately 80% with heat utilization, surpassing AE and PEM counterparts, which hover around 65%. According to the International Energy Agency (IEA), research and development efforts aimed at enhancing efficiency, through new materials or reversibility principles, could potentially push SOEC efficiency up to 90% by 2050. This potential increase in efficiency could significantly reduce LCOH, offering a substantial long-term advantage over AE and PE.
Durability
However, this heightened efficiency comes at a cost. The continuous exposure to extreme temperatures takes a toll on SOEC durability, primarily due to thermal stress. Current SOEC components struggle to maintain a long lifespan under these conditions, presenting a significant challenge for widespread adoption.
Presently, SOEC stack lifetimes are around 20,000 hours, one-third of PEM lifetimes and one-fourth of AE stack cells. The degradation rate for SOEC remains high, posing a hurdle compared to other established technologies. The IEA anticipates a threefold increase in SOEC lifetime by 2050, narrowing the gap with other technologies but not closing it.
Research and development efforts are actively addressing material durability issues. Various trends are emerging, such as exploring mixed ionic and electronic conductors for oxygen electrodes and different perovskite materials for fuel electrodes. Reversibility in SOECs, with consideration for electrochemical (EC) and fuel cell (FC) modes, is being examined, which could enhance the durability of electrode and electrolyte interfaces. There is also exploration into proton-conducting cells as an alternative to oxygen ion-conducting cells, as well as the potential benefits of lower-temperature solid oxide cells (below 500°C), which could unlock new materials and mitigate thermal degradation issues.
In summary, while the high-temperature operation of SOECs offers high efficiency, it also poses challenges for durability. The ongoing R&D efforts seek to strike a balance, addressing these challenges to harness the full potential of SOECs in the realm of hydrogen production.
Cost dynamics
As a nascent technology, SOEC is considered one of the most expensive types of electrolyzers, with capital costs ranging from USD 2,800 to USD 5,600 per kW according to IEA’s 2019 data. These costs are two to three times higher than those of PEM and AE. The high costs can be attributed to various factors, including the absence of large-scale manufacturing for these electrolyzers and the need for expensive raw materials to withstand high-temperature operation.
The high costs associated with SOECs can be attributed to several key factors. Firstly, SOECs require specialized high-temperature materials, which can be inherently expensive. Additionally, when compared to more mature technologies like PEM and AE, SOEC is relatively less developed, resulting in a steeper cost curve.
Even though the capital costs are currently estimated to be high, a high learning rate is estimated to be applied due to innovation in the technology itself. This high learning rate is estimated to reduce costs to USD 500–1,000 per kW by 2050. As mentioned above, these innovations are expected to involve the development of less costly materials for electrodes and membranes, as well as economies of scale in the manufacturing processes (for example, the development of larger stack sizes). These high learning rates will depend on deployed capacity over time. As the technology matures and becomes more widely adopted, the industry can look forward to more competitive pricing, making SOECs a compelling option in the realm of green hydrogen production.
Application fit
SOECs carve out a unique and promising niche in the realm of high-temperature applications. Their ability to utilize steam as a high-temperature heat source opens up many use cases, particularly in sectors like nuclear energy, solar thermal, steel, and geothermal operations. Additionally, SOEC systems align seamlessly with processes like the Fischer-Tropsch method, where waste heat can be harnessed to generate steam for electrolysis.
A 2018 study by the Union of Concerned Scientists shed light on the profitability challenges facing many US nuclear plants, with over a third of them deemed unprofitable or slated for retirement. Such profitability challenges intensify when natural gas prices plummet, or renewable electricity becomes exceedingly competitive. This is where the synergy between nuclear power and SOECs becomes truly captivating.
Leveraging nuclear power as an electricity source and tapping into its waste heat for hydrogen production can yield some of the most cost-effective and environmentally friendly hydrogen among its counterparts. SOECs, renowned for their high efficiency and operation at elevated temperatures, can be integrated into nuclear power plants to produce hydrogen at competitive costs.
What truly sets this synergy apart is the ability to integrate waste heat with SOEC technology, bolstering system efficiency by a remarkable 10–15%. Nuclear waste heat, valued for its low marginal cost electricity, often as affordable as USD 20 per MWh, aligns well with the ideal temperature range for SOEC, which hovers around 600°C. Placing these SOEC hydrogen production facilities in close proximity to nuclear facilities can emerge as a fitting strategy.
Similarly, the potential exists to integrate SOEC hydrogen production plants with industries such as steel, lime, glass, and more, all of which boast waste heat sources at ideal SOEC operating temperatures. As the learning curve for SOEC technology advances over time, these integrated projects hold the potential to deliver some of the most economical and environmentally friendly sources of hydrogen, while concurrently decarbonizing these crucial industrial sectors.
Key players and activities
Some of the key manufacturers of SOECs include Bloom Energy, Sunfire, Mitsubishi Power, and Topsoe. Currently, SOEC systems are typically limited to smaller stack sizes compared to AE and PEM systems. However, these leading companies have announced projects aimed at supplying higher-capacity-stack SOEC systems.
Bloom Energy has recently announced its involvement in the Nujio’qonik project, a significant USD 4.5 billion intercontinental green hydrogen commercialization initiative in Canada. This project, led by World Energy GH2 in Canada, aims to produce green hydrogen and green ammonia in Newfoundland and Labrador by 2025 and 2026, respectively. Bloom Energy boasts production lines with the capacity to manufacture 2 GW of SOECs annually. They claim their electrolyzers to be 45% more efficient than PEM and AE systems, making them a competitive choice.
Sunfire, another key player in the SOEC market, also asserts its efficiency, claiming its electrolyzers to be 20% more efficient than other types. Mitsubishi Power is set to supply solid oxide electrolyzers for a project that includes 220 MW electrolyzers with 40 units featuring a 5 MW stack cell size. Topsoe’s SOEC manufacturing plant passed FID stage for a capacity of 500 MW per year, with an option to expand to 5 GW.
About the author
