By Dr. Johanna Steinbock, Jan Sachse and Dr. Albert Großmann, TÜV SÜD Industrie Service
Hydrogen generated with electricity from renewable sources could save several million tons of CO2 emissions each year in Germany alone. In addition to its use in the steel or chemical industry, the energy carrier is suitable as an electricity storage medium and for fuel cell drives in the transport sector. Against this background, the German Federal Ministry for Economic Affairs and Climate Action and the Federal Ministry for Digital and Transport have been funding around 60 large-scale hydrogen projects since mid-2021 with a total of more than €8 billion – from generation to transport to industrial application.
Using existing infrastructure
With a service life of up to 100 years, pipelines and cavern storage facilities are particularly ecological and economical solutions for the transport and storage of gas. In addition to around 500,000 km of natural gas lines for regional and local distribution in Germany, about 40,000 km are used for nationwide and cross-border transport. The pipes with diameters of up to 1.4 m and operating pressures of up to 100 bar are in principle also suitable for transporting hydrogen, which the past has shown. Using the existing infrastructure would make the switch to hydrogen as an energy carrier even more sustainable. However, it is essential to examine in detail and according to the current state of the art how hydrogen affects different steels. Adapted safety and maintenance concepts must also be developed.
Embrittlement of the material
In high-strength steels, there is a risk of hydrogen-induced cracking. The smallest defects in the steel structure, inclusions and impurities – sometimes in combination with mechanical stresses – break down protective oxide layers of the metal so that hydrogen atoms diffuse into the material and accumulate to defects in the lattice structure of the steel. Damage to passivating oxide layers cannot be avoided permanently, as pipelines – particularly long-distance ones – are exposed to operational changes of the internal pressure. There are various reasons why the internal operating pressure of a pipeline varies, such as feeding and discharging processes.
The hydrogen absorption impedes the plastic deformation capability of the material and consequently leads to a decrease in ductility. The material becomes brittle and microscopically fine cracks develop. Due to the further concentration of hydrogen at the crack tip and load changes, the crack grows. The extent of hydrogen embrittlement depends on the steel grade, its microstructure composition and manufacturing method. Higher strength values and rougher surfaces increase the risk of hydrogen embrittlement. In general, hydrogen reduces fracture toughness by up to 50% and accelerates the growth of cracks – even at relatively low partial pressures. It also lowers the elongation and the reduction of area but does not affect tensile strength.
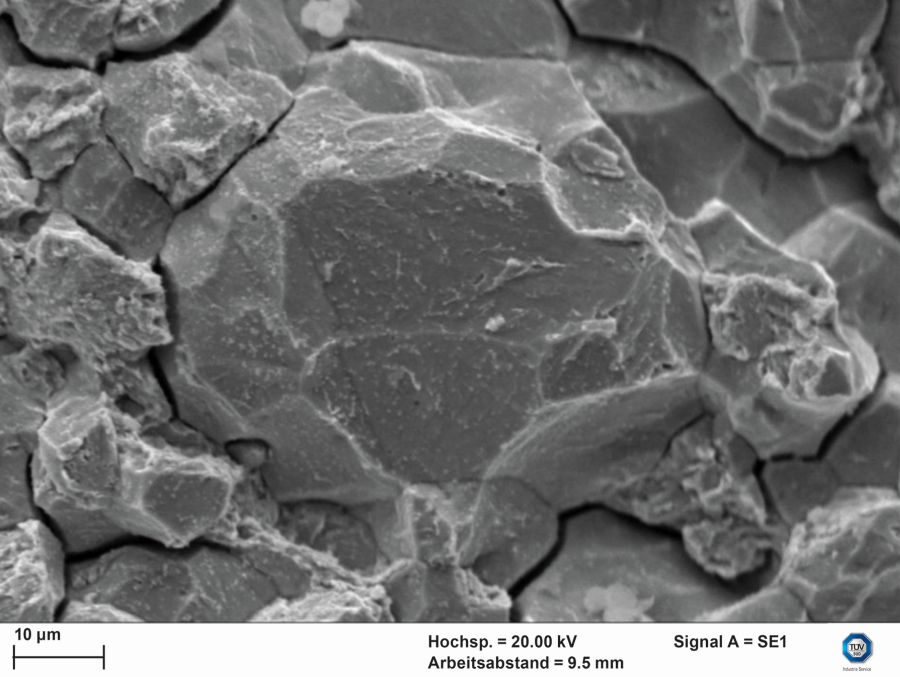
Evaluating risks with fracture mechanics
With the application of fracture mechanics, the pipelines and their materials are examined for their suitability to transport hydrogen. In addition, the expected service life of hydrogen transportation infrastructure can be calculated. In the event of known damage in existing pipes, the experts assess the component integrity. But fracture mechanics is also used for new pipelines. With its help, the detection limits of the non-destructive testing of the material and the weld seams can be determined, and the intervals for the periodic inspections for future operation can be calculated.
The fracture mechanics calculation principles allow to determine the growth behaviour of cracks. In addition to the material-specific parameters, stresses and interaction to environmental media are considered. The basis for the crack growth analysis are the principles of linear elastic fracture mechanics, which assume that the stress at the crack tip is theoretically unlimited such that the factors stress intensity and energy release rate describe the local stress state at the crack tip and the behaviour during crack growth.
Since hydrogen diffuses into the metal lattice over time, the frequency at which the material is under load also plays an essential role, especially since load changes due to fluctuating operating pressures can additionally promote crack growth. At a high operating pressure with the smallest pressure amplitude, less crack growth can take place than at a lower operating pressure but larger pressure amplitude.
Visualisation in the diagram
Using the Failure Assessment Diagram (FAD), damage (cracks and crack-like flaws) that can lead to the failure of components is considered holistically and evaluated in terms of fracture mechanics. The factors load intensity (Lr) and stress intensity (Kr) describe the impact on the component with regard to plastic failure of the residual cross-section and the stress state at the crack tip with regard to brittle failure. Lr indicates the ratio of the existing stress in the residual cross-section to the maximum load-bearing capacity (the collapse load). Kr corresponds to the ratio of the existing stress state at the crack tip (the stress intensity) to the fracture toughness applicable to the material.
Together, Lr and Kr define the location of an evaluation point in the FAD (see Figure 2). The green FAD limit curve separates the acceptable crack size at the bottom from the unacceptable crack size at the top. The blue point represents a concrete case of evaluation. Based on an analysis of past load cycles, considerations for future load cycles can be derived. Then the crack growth to be expected for an initial defect until the maximum allowable defect size is reached can be determined by calculation – and thus what service life for the pipeline can be expected.

Clarifying how H2 affects materials
In the USA, steels listed according to the ASME Code have been widely studied, so their fracture-mechanics parameters under exposure to hydrogen are well known. For individual steels, however, fracture resistance and fatigue crack growth under the influence of hydrogen have not yet been determined, or certain alloy components or heat-treatment processes can change these parameters.
Particularly for European materials, fracture mechanics can only be verified once the specific influence of hydrogen on these parameters has been determined. The German Association of the Gas and Water Industry (DVGW – Deutscher Verein des Gas- und Wasserfachs e. V.) has launched a research project on this subject. TÜV SÜD sits on the relevant committees to discuss and develop the associated safety concepts.
Normative bases
In Germany, the Energy Industry Act (EnGW – Energiewirtschaftsgesetz) must always be observed for gas pipelines – regardless of whether they transport natural gas, pure hydrogen or a mixture. According to the Ordinance on High Pressure Gas Pipelines (GasHDrLtgV – Gashochdruckleitungsverordnung), the conversion of existing natural gas pipelines to hydrogen operation constitutes a significant change and must be notified. The operator must prove that the conversion was carried out in accordance with the current state of the art and in a professional manner. The technical requirements and the current knowledge are described in the DVGW standards G463 and G409.
Obtaining neutral expertise
TÜV SÜD is currently examining the conversion of existing natural gas pipelines to hydrogen for pipeline operators. The experts consider all influences on the service life as well as the documents for planning, construction and operation. They also show which measures are suitable for determining, assessing or upgrading the condition of a plant. TÜV SÜD provides support with safety concepts and fracture mechanics analyses for a safe and CO2-neutral energy industry.