Current state of hydrogen storage technology
A large portion of clean hydrogen will not be consumed at the same time and location where it is produced – a very different setup than the majority of old (gray) hydrogen projects in the past few decades. Long-term, seasonal storage of hydrogen is key to several use cases and applications in the hydrogen economy. Countries like Germany, Japan, and South Korea are planning to import 85–90% of their hydrogen.
All conventional hydrogen storage technologies (compressed hydrogen, liquified/cryogenic hydrogen, ammonia) as well as more modern technologies, including liquid organic hydrogen carriers (LOHC), require extreme conditions of compression and/or temperature. In order to reach those very high or very low temperatures and/or high compression, significant amounts of energy are required, sometimes reaching up to 13 kWh or even above 40 kWh to store and release one kilogram of hydrogen. The result: poor energy efficiency and very high OpEx costs, much above industry targets.
Most technologies even require maintaining these temperatures and/or compression levels over time, which increases their energy costs to huge levels for long-term, seasonal storage.
Moreover, all these technologies involve the use of toxic, flammable and/or explosive materials – having at least two of these three characteristics. The result: very high CapEx and ongoing maintenance are required to make this infrastructure relatively safe and comply with regulations. In many cases, such storage is even prohibited in populated areas. The complexity of handling and operating hydrogen projects in the industry today is very often related to this safety challenge.
The high OpEx and CapEx, along with the hazardous/cumbersome/regulated supply chain, pose clear obstacles in scaling up the hydrogen economy and contribute to related risks. The levelized cost of hydrogen, storage, and transportation often reaches double-digit figures in dollars per kilogram of hydrogen – far above the industry’s target of USD 2–3 per kilogram of green hydrogen, including production and storage/transportation.
Catalytic and circular reaction
At the crossroads of advanced chemistry and materials engineering, Hydro X has developed a revolutionary technology that enables the reinvention of the conventional way of storing and transporting hydrogen. This is achieved through a catalytic and reversible reaction, using formate and bicarbonate salts in a catalytic cycle:

The process involves the chemical charging of hydrogen on bicarbonate salt (a commercially available material commonly known and used as ‘baking soda’) using metal a catalyst, and converting it into an aqueous solution – the hydrogen-charged liquid – containing water and formate salt, another commercially-available material commonly used for non-corrosive de-icing of airplanes wings.
When and where needed (and it could be months after and thousands of kilometers away from the charging location), the stored hydrogen can then be extracted on demand from the charged liquid instantly, converting it back into the original discharged liquid, ready for new hydrogen loading.
Non-toxic, non-flammable, non-explosive
Both charged and discharged liquids are water-based, non-toxic, non-flammable, and non-explosive materials.
The formate-salt-solution hydrogen carrier can be stored and transported in standard water tanks, water pipes, and even plastic tanks or leveraging existing oil infrastructure, setting new standard in terms of safety, operations, maintenance, and regulation. The result: significantly lower CapEx costs for hydrogen infrastructure.
Unparalleled energy efficiency
Charging is done at 35°C and 10 to 20 bar, and discharging at 50°C and atmospheric pressure, 1 bar. These close-to-ambient conditions require a very small amount of energy, 2–2.5 kWh per kilogram of hydrogen stored and released, which represents around 94% energy efficiency.
Some other most modern technologies require temperatures of 300°C or even higher, low liquefaction temperatures ranging from -33 to -253°C, and/or compression levels hundreds of times higher than atmospheric pressure. These extreme conditions lead to energy consumption of 13, 14, or even 40 kWh (more than the energy content of 1 kg of hydrogen!) to store and release one kilogram of hydrogen.
The result: <USD 1 per kilogram of hydrogen OpEx cost for the round trip (charging + discharging).
Due to the relatively low required temperature (35–50°C) and pressure (10–20 bar), this energy requirement can be further reduced by using heat produced by a nearby electrolyzer, fuel cell, or other equipment with extra heat and pressure.
Benefits for (long-term) stationary storage of hydrogen
One of the main use cases in the hydrogen economy is long-term storage, spanning day-, week- and even month-long periods. This includes buffering or back-up for chemical, iron and steel, and other heavy industries, hydrogen and gas-blending turbines, seasonal energy storage for renewable energy fields, as well as for factories, data centers, and other distributed facilities in urban areas.
Conventional technologies require maintaining some temperature/pressure conditions during the storage period, which requires significant amounts of energy over time. Moreover, the safety risks result in expensive periodical safety maintenance and high CapEx costs. When the use case involves long-term, seasonal (e.g., summer to winter) storage of hydrogen, the storage OpEx costs grow linearly to very high levels, and the CapEx costs are amortized on smaller amounts of hydrogen.
By contrast, formate-bicarbonate cycle-based technology does not require maintaining any specific temperature or pressure during the storage period. No safety maintenance or high CapEx is required due to its non-toxic, non-flammable and non-explosive characteristics. The result: flat costs, around the USD 1 per kilogram of hydrogen, regardless of the length of the storage period.
Benefits for hydrogen transportation
The safety risks associated with conventional technologies result in the need to use special, dedicated, expensive, and highly regulated trucks, ships, trains, or pipelines to transport hydrogen.
Using formate/bicarbonate aqueous solutions enables the transportation of hydrogen in plastic tanks on regular trucks driven by drivers with standard driving licenses, with no limitations related to tunnels or underground parking.
It also enables the transportation of hydrogen through water pipelines, which are 3–5 times cheaper than gas pipelines usually used to transport gaseous hydrogen (compressed at 40–100 bar). Such pipelines do not require complex maintenance and monitoring as a leakage does not pose any environmental risks as seen in other technologies.
Last but not least, formate and bicarbonate salts and aqueous solutions offer a much cheaper and safer alternative to ammonia for long-distance ship transportation.
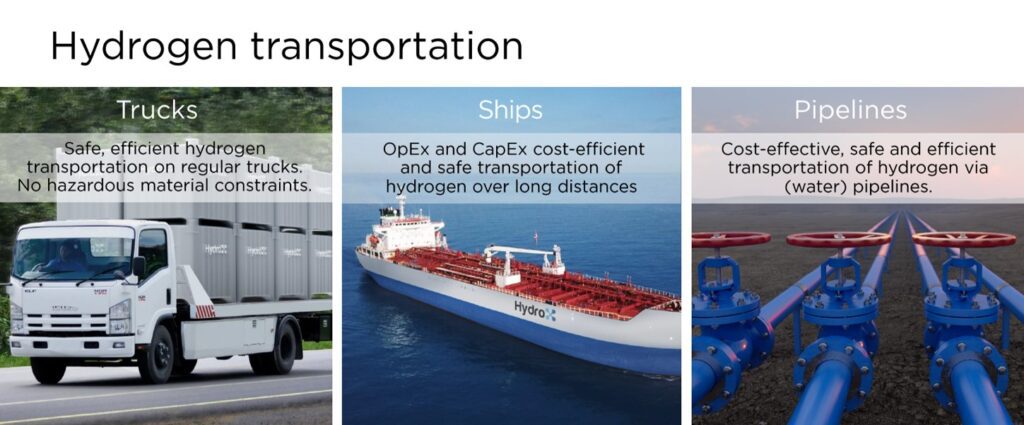
Ammonia involves huge energy waste throughout the entire process, from the conversion (Huber-Bosch process for converting hydrogen to ammonia), through the transportation itself, which is done in a liquified form at -33°C, down to the cracking (from ammonia back to hydrogen). All in all, this results in an energy waste of at least 34%, and up to 60% as mentioned in a recent report by the International Renewable Energy Agency (IRENA).
Ammonia requires special and expensive ships with specific equipment. The typical ammonia ship has a capacity of 20,000–30,000 m3. The largest ships are planned to be 80,000 m3, much smaller than typical 300,000 m3 oil tankers.
Ammonia is inherently extremely dangerous. To mitigate the risk and make ammonia relatively safe, huge CapEx investments are necessary, including very expensive and special tanks, as well as heavy and complex equipment. Some phases of the process (especially the cracking part) are relatively young and not yet mature technologies.
Hydro X liquid (based on formate and bicarbonate solution) allows the use of completely standard ships (including oil tankers, very large dedicated ships, or a small space on a large ship), very cheap tanks, and affordable equipment to store and transport hydrogen by oceans, at unparalleled energy efficiency.
Despite a weight density resulting in the transportation of significantly more weight than ammonia for the same quantity of hydrogen, formate salt (e.g., potassium) is almost four times cheaper OpEx-wise (including ship transportation costs) and more than four times cheaper CapEx-wise compared to ammonia, which is currently considered the leading technology for similar projects. This adds to a disruptive safety advantage, which translates into project derisking and sustainability.
Conclusion
The multiplication of large industrial-scale projects involving the storage and transportation of hydrogen requires various technologies to play different roles at different stages of this international market. Nevertheless, in the context of scaling up the hydrogen industry and reducing the related safety and financial risks, the adoption of disruptive, energy-efficient and completely safe technologies like that developed by Hydro X is key to unlocking the hydrogen economy.