By Thorbjoern Fors, Executive Vice President, Industrial Applications, Siemens Energy
The International Renewable Energy Agency (IRENA) projects that hydrogen and its derivatives could account for up to 12% of worldwide energy consumption by 2050.1 Meeting this demand sustainably will require significant growth in the production capacity of both ‘blue’ and ‘green’ hydrogen.
Green hydrogen holds enormous potential as a decarbonization agent by serving as a stable carrier and chemical storage medium of clean energy produced by renewables and as an input for carbon-neutral e-fuels, such as eMethanol and eAmmonia. However, there are still hurdles to overcome on the way to creating a sustainable and prudent green hydrogen economy.
First, the cost of producing green hydrogen must be reduced dramatically. While the levelized cost of energy (LCoE) has the most considerable influence on overall project economics, the efficiency of the production plant itself is also important. To this end, developers must be strategic when selecting energy-intensive equipment, such as compressors and electrolyzers. A holistic development approach is also required to ensure that processes are optimized around operational constraints to maximize production and revenue over the facility’s life.
Compressor considerations
Reciprocating and centrifugal turbocompressors are the two primary means of compressing hydrogen today. Both have demonstrated success in a wide range of industrial applications.
Reciprocating compressors work on the principle of positive displacement, which means that compression efficiency is unaffected by the low molecular weight of hydrogen. As a result, even at partial loads (down to 50%+), efficiencies as high as 90% can be achieved.2
Generally speaking, reciprocating compressors can achieve higher compression ratios in fewer stages than turbocompressors. However, the efficiency advantage of reciprocating machines can diminish at high flow volumes. Because of this, turbocompressors are more often applied in moderate- to high-flow applications with lower pressure ratios. Reciprocating compressors, on the other hand, are better suited for high-pressure applications with lower volumes. A prime example is a green hydrogen plant.
In most conventional applications where reciprocating compressors are used (e.g., pipeline compressor stations, refineries, etc.), the machines are typically required to operate continuously without interruption. As a result, a high priority is placed during the design process on maximizing reliability and extending the mean time between failures (MTBF) to prevent downtime and the resulting production loss.
Due to the nature of renewables, such as wind and solar, green hydrogen plants are designed to run intermittently and at part load for extended periods. Therefore, given the operating profile, it is advantageous to focus on compressor reliability while prioritizing other attributes that contribute to energy efficiency and power consumption. Among these attributes are:
Capacity Control. Capacity control is a crucial factor to consider when designing a compressor for a green hydrogen plant, as it impacts the ability of the machine to perform its duty efficiently under highly variable conditions.
Several capacity control methods are available for process reciprocating compressors. Plug, port, or finger unloaders, for example, can be used to unload compressor cylinder ends, facilitating 100% capacity and 50% capacity with a corresponding reduction in power consumption.
Another option is using pneumatically actuated fixed volume clearance pockets, which increase cylinder clearance and reduce capacity without losing the energy of compression. If variable capacity is required, hydraulic variable volume clearance pockets can be implemented to dynamically adjust cylinder clearance during operation, controlling compressor capacity and limiting consumed power.3
The optimal choice of capacity control will depend on operator requirements/preferences concerning CAPEX, OPEX, and turndown requirements.
Compressor Valves. Improper valve selection can result in higher compressor power consumption, as more energy is needed to open suction and discharge valves so gas can flow into and out of cylinders. Preventing this requires early collaboration between the plant operator and compressor OEM to implement valves that are (1) designed for hydrogen gas and (2) minimize excessive differential pressure. Once the operating pattern of the compressor has been defined, valves can be customized to meet expected performance during nominal plant operation while also guaranteeing acceptable performance in the event of certain abnormal circumstances.
Driver Selection. With efficiencies of >95%, slow-speed electric motors are the preferred driver of reciprocating compressors. However, the specific type of motor selected can significantly impact energy consumption. For example, synchronous motors are roughly 1–2% more efficient than the induction equivalent and are often utilized for compressors with high power ratings (i.e., over 1,500 kW). Other advantages include reduced utility fees through reduced peak demand, elimination of power factor penalty, increased system capacity, and higher voltage levels in the electrical system.
Electrolyzer efficiency
Electrolyzers are the most significant power consumer in a green hydrogen plant. Their efficiency is therefore vital to keep operating costs down and maximize revenue.
Various measures are used to calculate the efficiency of electrolysis. Faraday efficiency, for example, is the ratio of the actual usable volume of hydrogen produced and the theoretical maximum production volume. On the other hand, DC efficiency is the ratio of the energy input (measured as DC current) to the electrolyzer stack/module and the energy content of the technically usable hydrogen at the stack output.4
While these efficiency metrics are generally accepted across the industry, total plant efficiency is often defined arbitrarily. Depending on the plant, losses can occur due to the conversion of electricity from AC to DC or from voltage transformation. Water treatment and cooling systems, along with the use of power for buildings, compression packages, and hydrogen purification, also impact overall efficiency.
When designing a plant, developers must take a holistic approach that examines how all systems and auxiliaries can be optimized around any potential process constraints or bottlenecks. This starts by defining system boundaries and standard conditions. The ultimate objective should be to strike a balance that enables the lowest cost of hydrogen production while simultaneously providing maximum uptime and availability for the operator over the long term.
Making projects reality
As previously stated, LCoE has the most considerable influence on the viability of green hydrogen production. As real-world projects have shown, under favorable conditions (i.e., LCoE of US$20/MWh and ~6,000 full-load hours), green hydrogen generated from electrolysis can reach cost parity with grey and blue hydrogen produced via steam-methane reforming or autothermal reforming of natural gas.5 For plants where green hydrogen will be combined with CO2 to create climate-neutral eFuels, such as eMethanol, the cost of carbon capture also impacts project economics.
There are now several regions around the world where a strong business case can be made for green hydrogen and/or eFuel production. Large-scale projects are already in development, with more planned in the coming years.
One notable example is the Haru Oni project in Chile, where Siemens Energy is planned to provide the electrolyzer – a Silyzer 200 – as well as overall plant integration for the world’s first integrated and commercial-scale plant to produce green hydrogen and methanol-based eGasoline. Downstream of the electrolyzer, the green hydrogen will be combined with CO2 collected via direct air capture (DAC) to produce synthetic methanol. A pilot plant is initially being built and is expected to produce around 130,000 liters of eFuels in 2023. Plans are to expand the capacity in two stages to approximately 55 million liters by 2025 and about 550 million liters by 2027.
Another recent example is Liquid Wind’s FlagshipONE eMethanol project in Sweden, which will be the first of as many as 500 standardized eMethanol plants that Liquid Wind plans to develop over the next three decades.6 At the facility (the first of its kind, in Örnsköldsvik, Sweden), as much as 70,000 tons of biogenic CO2 per year will be captured and combined with green hydrogen to produce 50,000 tons of carbon-neutral eMethanol. The methanol will replace hydrocarbon fuels in shipping operations, preventing the emission of approximately 100,000 tons of CO2 per year.7
Siemens Energy is providing the 70 MW Silyzer electrolyzer for the plant, along with power distribution infrastructure, instrumentation, motors, drives, plant-wide automation, and digital solutions, including the process, data and operations digital twins.
The road ahead
Green hydrogen is poised to play an essential role in the energy transition and holds enormous potential in decarbonizing emission-intensive sectors, such as the transport and process industries. However, the availability of low-cost renewable electricity is the most significant constraining factor preventing the large-scale build-out of green hydrogen capacity.
It is estimated that in Europe alone, up to 1,300 GW of dedicated renewable generating capacity will be needed by 2050 to fulfill green hydrogen demand. In addition, more than 500 GW of new electrolyzer capacity will also need to be installed.8 Fortunately, the world is on the right path. IRENA projects that global renewable energy capacity could quadruple by 2030.
Expanding the range of business cases will also require bringing down the cost of developing and operating green hydrogen production/eFuel plants. Achieving this requires solid partnerships and co-creation between developers, OEMs, and operators early on to optimize equipment arrangements and take steps to maximize plant efficiency. Governments also have an essential role to play by instituting policies that foster innovation and investment that further stimulates the pipeline of real hydrogen projects.
Only by working together can we unlock the full potential of green hydrogen as a decarbonization agent and drive a successful energy transition.
About the author
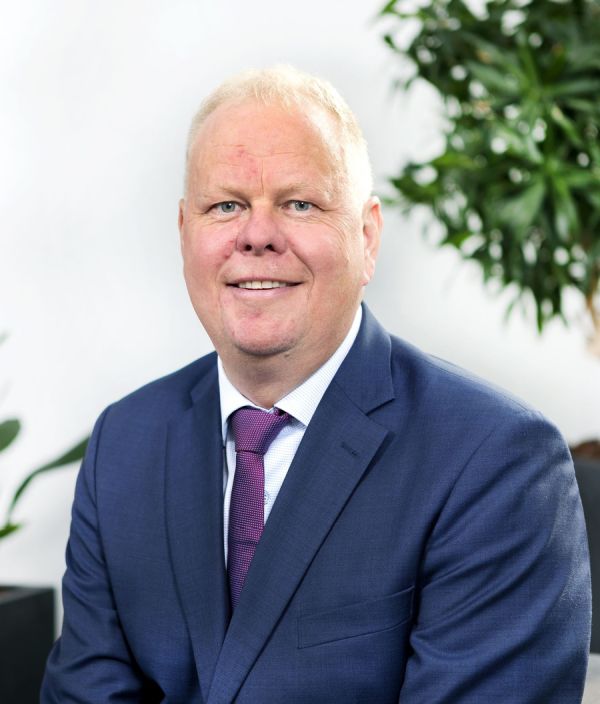
Thorbjoern Fors is the Executive Vice President of Siemens Energy’s Industrial Applications division. Prior to this position, he served as CEO of the Service Distribution Generation and Oil and Gas business unit of Siemens. He also held EVP roles in the organization’s industrial power generation and compression business and within global marketing and sales of new equipment. Mr. Fors is a mechanical engineer with more than 25 years of international experience in business development, sales, operations, and leading global businesses.