By David Sear
In his home city of Leiden in the Netherlands, Mr van Schooneveld is held in high esteem by quite a number of grateful homeowners. For as a volunteer “energy coach” working for the city council, he helps people to identify and prioritize ways to reduce energy consumption. It is a task Mr van Schooneveld finds extremely rewarding, having seen at first hand the benefits that can accrue from, just to give some examples, improving home insulation, replacing inefficient domestic appliances and installing solar panels. In fact, in a space of just five years, he has slashed total energy consumption at his own home by over fifty per cent, saving money of course but also reducing his family’s carbon footprint in the process.
Mr van Schooneveld is using his same skill for refining complex theory into easily understandable words to present the next generation of electrolyser anodes. And yes there is a direct parallel with his voluntary work as these anodes can help to drive down the cost of green hydrogen significantly.
Speaking to Hydrogen Tech World, Mr van Schooneveld kindly outlined his company’s credentials. “Magneto Special Anodes has been developing and manufacturing anodes since 1957 and has built up a strong presence in the fields of water treatment, electrolysis, cathodic protection, metal plating, and electrowinning and recovery. In short, we have a deep understanding of anodes in a variety of applications. We also appreciate our customers’ needs; they are looking for anodes that will of course function well but also offer durability. In other words, the ideal anode should be able to pass a high current density without dissolving, disintegrating, corroding or otherwise exhibiting a drop in performance.”
Durability a top priority
Having slowly but surely been building up its presence in the broader hydrogen sector for many years, Magneto took the decision to become much more proactive as regards anodes for green hydrogen production in 2019. Comments Mr van Schooneveld : “We immediately initiated a robust research and development programme which has quickly paid dividends. Right now for example we can already provide components for PEM stacks and are working towards market entry with a number of anode product forms, including meshes, felts and foams. In fact, I am already discussing our products with parties all along the green hydrogen supply chain, including the stack builders, the EPCs who are responsible for the complete systems, the principals, etc. I can say that a lot of possibilities are opening up.”

Understandably, Mr van Schooneveld is not about to reveal all the technical secrets behind Magneto® anodes for hydrogen production. Suffice to say that it is the coatings that play a key role. This is because uncoated anodes – which are the current industry standard – are known to suffer from decay and cannot pass higher current densities.
“Generally speaking, anode coatings perform one of two functions. They either act as a catalyst, or are applied to improve durability and performance. Our discussions with the stack builders indicated that enhanced durability was their key priority so that has naturally been our focal point to date. Thanks to our extensive knowledge of anode materials but also the technology needed to apply coatings, we have been quickly able to develop a coating which can extend anode life two-fold. Moreover, because we deliberately avoid using any expensive PGM alloys – that’s short for platinum group materials – our coating is available at very little extra cost.”
With a more durable anode, stack builders can realise significant CAPEX or OPEX benefits, indicates Mr van Schooneveld “If you compare two equally sized electrolysers, one made using standard anodes and one with our coated anodes, then the latter model will be much more efficient as it can produce twice as much hydrogen. So your OPEX costs will be lower per quantity of hydrogen produced.
Alternatively, if you require a specific hydrogen output, then the use of coated anodes means that the stack and indeed the rest of the facility will be smaller. And that can translate into a significant CAPEX saving.”

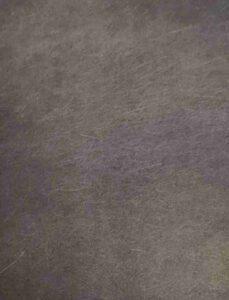
Mr van Schooneveld is therefore looking to the future with considerable optimism. Not just in terms of the business potential for Magneto, but also how coated anodes could help position green hydrogen as a way to achieving much lower carbon emissions. “As we speak the industry is looking to scale up the production of green hydrogen. However, there is also a clear need to drive down prices, as green hydrogen currently costs three times more than hydrogen produced from fossil fuels. We have demonstrated that our coated anodes can improve electrolyser performance and are therefore looking forward to increasing our deliveries of these quality components that really can make a difference.”