When describing a green hydrogen production plant, what elements come to mind? A hydrogen production facility, particularly one dedicated to green hydrogen, is a complex assembly of systems and infrastructure designed for environmentally friendly hydrogen fuel production, storage, and management. Figure 1 outlines the major streams and components of a green hydrogen production plant.
At the heart of the facility lies the electrolyser system, which splits water into hydrogen and oxygen using electricity – sourced ideally from renewable energy to maintain the hydrogen’s ‘green’ label. This system comprises stacks (individual cells combined for the electrolysis reaction) and units (assemblies of these stacks). The balance of system (BoS) encompasses additional elements essential for the electrolyser’s operation, such as transformers and rectifiers for AC to DC power conversion, and a control system for process management.
Civil works, including construction of equipment housing, lighting installation, and access road development, are also vital.
The control system is an overarching element that ensures all parts of the plant operate harmoniously and efficiently. It monitors and adjusts the processes within the electrolyser system and the BoP to maintain optimal performance.
The balance of plant (BoP) is a broad term encompassing the subsystems necessary for the plant’s operation, such as high-voltage transformers for power level adjustments, a water treatment plant for purifying water for electrolysis, and cooling systems to dissipate heat generated during the process, especially in low-temperature electrolysis technologies. Also critical are nitrogen and air supply systems for creating an inert atmosphere when needed and meeting various operational requirements. Compressors are used to increase the pressure of the hydrogen gas for the end user, storage, or transport. Lastly, hydrogen storage is an essential part of the infrastructure, allowing for the accumulation of produced hydrogen until it is needed by the off-taker.
Each component is crucial for the efficient and sustainable operation of a green hydrogen plant, necessitating careful integration. This article will delve into the specifics of BoP components, offering insights into their importance and integration for effective plant operation.
Balance of plant: understanding the inner workings
To meet off-taker specifications, a hydrogen production plant must integrate several components, ensuring hydrogen purity, correct pressure, and suitable temperature for transport and usage. Figure 2 highlights key BoP components, emphasizing the necessity of compressors and storage systems, which vary in need across hydrogen plants.
High-voltage transformers and power connection
The electrical power connection requirements for hydrogen plants vary based on the plant’s size, operational needs, and the country’s available power infrastructure. For instance, a 10 MW plant in Denmark typically connects at 10 kV, while a 1 GW plant may connect at 400 kV. As hydrogen projects scale, specialized electrical designs are required to manage costs and incorporate additional components like transformers and switchgear. Switchgear plays a crucial role in the safe and efficient operation of a hydrogen electrolysis plant, managing and protecting the power distribution system and ensuring a stable electricity supply. It encompasses various types of switchgear for power supply, distribution, control, and protection, as well as communication and monitoring systems for data and remote control. These systems are essential for safety, particularly given hydrogen’s flammability. It is important to note that the costs for additional power requirements, such as large transformers and extra switchgear, are not typically included in the initial capital expenditure (CAPEX) estimates.
Water treatment plant
The water electrolysis process for hydrogen production requires high-quality water to prevent contamination and undesired byproducts. Different water sources, such as groundwater, surface water, and seawater, necessitate varying pre-treatment methods due to their distinct mineral and contaminant profiles. The volume of water required for treatment varies by source, with ratios indicating that more raw water is needed to produce ultrapure water essential for electrolysis. The treatment process typically includes a pre-treatment phase and a polishing step, determined by the water source and electrolyser technology, respectively. This process may involve multiple stages, including filtration, aeration, UV treatment, desalination, softening, demineralization, degassing, and polishing through Electrodeionization (EDI).
Cooling system
Cooling systems play a pivotal role in the production of green hydrogen, particularly during the Alkaline Electrolysis Cell (AEC) and Proton Exchange Membrane Electrolysis Cell (PEMEC) stages. The heat generated during these processes can lead to damage and reduced efficiency if not properly managed. By utilizing a combination of coolants, heat exchangers, and advanced cooling techniques, such as liquid cooling, these systems ensure the electrolyser operates within the optimal temperature range. This not only contributes to the stability and durability of the components but also enhances the overall efficiency of the hydrogen production process. Maintaining the correct operating temperature is essential for the long-term success and sustainability of green hydrogen as a clean energy source.
Nitrogen and air supply
Ensuring the proper operation of a green hydrogen plant involves precise management of nitrogen and air supply. Nitrogen, often used as a purging gas, helps maintain a non-reactive atmosphere, crucial for the safety and efficiency of the hydrogen production process. Air supply, on the other hand, is used for the instrumentation of much of the plant’s equipment. Policies and guidelines, such as those suggested by IRENA, provide a framework for optimizing operations, addressing challenges like integrating sustainable electricity sources and managing the hydrogen supply chain.
Further purifier/dryer equipment
In the context of green hydrogen production, purifiers and dryers play a crucial role in ensuring the quality and efficiency of the operation. Purification systems, such as Pressure Swing Adsorption (PSA) technology, are used to separate hydrogen from other gases produced during electrolysis. Dryers, on the other hand, remove moisture from the hydrogen gas, which is essential for preventing corrosion and maintaining the integrity of the infrastructure. These elements are important to consider when designing or upgrading a green hydrogen plant to ensure its optimal operation, longevity, and delivery of hydrogen with the correct specification to the off-taker.
Compressors
Compressors are a critical component in hydrogen plants, ensuring the delivery of hydrogen at the required specifications for the off-taker. The type of compressor used can significantly influence both CAPEX and OPEX of a hydrogen plant.
Several types of compressors are used in hydrogen plants, including reciprocating piston compressors, screw compressors, and diaphragm compressors. Each type has its own set of characteristics that can impact the overall costs of a hydrogen plant. For instance, reciprocating piston compressors are widely used and are known for their reliability and efficiency in high-pressure applications. Screw compressors, on the other hand, are more suitable for lower pressure ranges and can offer economic advantages, especially with increasing volume flows and fluctuating operating conditions.
The choice of compressor technology is project-specific and requires a balance between technical and economic considerations. For example, reciprocating compressors are typically applied in applications with small suction volume flows, high pressure ratios, or high process flexibility requirements. In contrast, centrifugal compressors are better suited for low compression ratios and medium- to high-volume flow applications but have a higher risk of ‘low density hydrogen gas’ leakage via the shaft seals.
Hydrogen storage
Hydrogen storage and transportation are critical for its use as a fuel source, necessitating methods that are safe and efficient. Gas compression and cryogenic liquefaction are physical methods used to reduce hydrogen volume and store it at low temperatures, respectively, although they are energy-intensive. Chemical carriers such as LOHC, ammonia, and methanol offer alternative storage solutions. Material-based storage, including metal hydrides and sorbent materials, provides storage at near-ambient conditions, potentially increasing energy density but with challenges in weight, cost, and hydrogen release rates. Large-scale storage options like salt caverns are also considered for substantial, long-term hydrogen storage. The choice of storage system varies based on project needs, location, and the specifics of the end user, influencing the overall cost estimation.
Understanding CAPEX through BoP component identification
Ramboll’s research indicates that accelerating the deployment of green hydrogen projects involves more than merely increasing electrolyser manufacturing capacity. By strategically addressing specific technological aspects, substantial reductions in CAPEX become feasible. Direct costs constitute a significant portion – between 75% and 90% – of the total estimated installation costs, as determined by Ramboll. These direct costs, including expenses related to stacks, compressors, and electrical equipment, account for 60% to 90%, depending on the technology used. To achieve the anticipated reduction in generation facility costs within the green hydrogen community, Ramboll recommends focusing on key areas: standardizing components, defining interconnection processes, and harmonizing regulatory frameworks across borders. These measures are essential for achieving sustained CAPEX cost reductions over time in green hydrogen production plants.
References
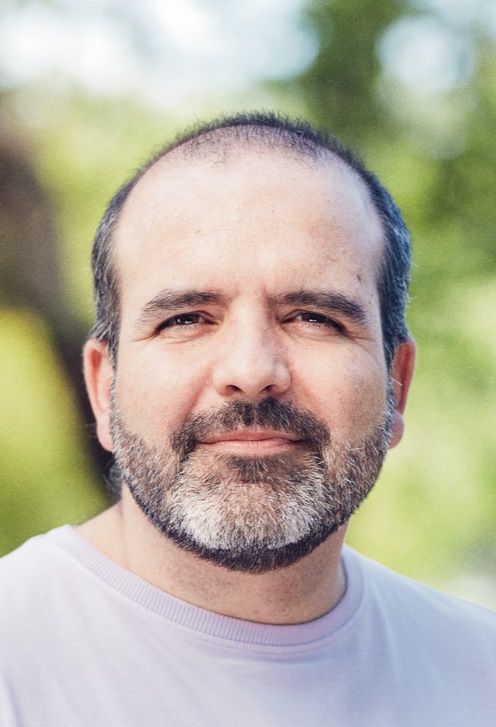